LG Display is currently the only one in the world to produce large size OLED panels for TVs. Degree of difficulty in manufacturing large size OLED panels (2200x2500mm) while being cost-effective and using organic matters that are vulnerable against water and air is significantly high. Large size OLED panel is also the index that represents the position of South Korea’s OLED technology. YAS (CEO Jung Kwang-ho) is an equipment manufacturer that is one of key partners of LG Display that had contributed to commercialization of Gen 8 OLED panel. It developed and commercialized 8th generation deposition equipment that is a key front-end process equipment for OLED manufacturing process. Currently, Canon Tokki and YAS have the upper hands within markets for Gen 6 OLED deposition equipment and Gen 8 OLED deposition equipment respectively. Although many South Korean equipment manufacturers have jumped into the market for Gen 6 OLED deposition equipment and supplied their equipment for mass-production purpose, Canon Tokki still holds the stronghold within the market. On the other hand, YAS is the only one in the world to manufacture Gen 8 deposition equipment. Key technology for YAS’ Gen 8 deposition equipment is an ability to control ‘large size glass substrate’. There is not much difficult to transport and lift large size LCD glass substrate as it is transferred under normal atmospheric pressure. On the other hand, deposition process for OLED panel takes place under vacuum. 2200x2500mm glass substrate needs to be lifted inside of a large vacuum chamber and it needs to be flipped after transferring it through many chambers. Because thin glass substrate can droop to the bottom due to gravity, there needs to be a design that considers this issue.
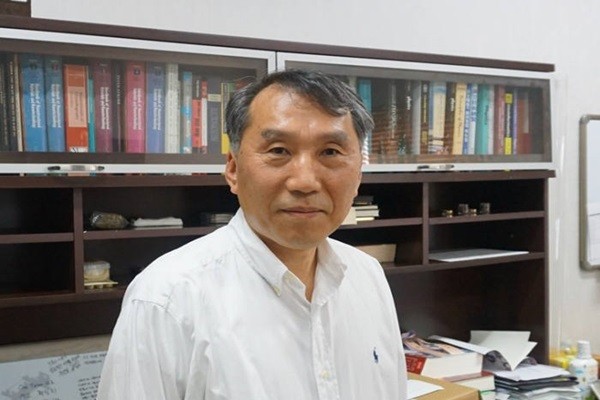
There can also be an issue when a glass substrate can fall to the bottom when it is lifted by holding its sides due to vacuum state. Because a glass substrate can be faulty when there is physical contract to the top of a glass substrate where pixels are formed, technology that can steadily transfer glass substrates under vacuum state is needed and this technology is very intricate. YAS developed sticky chuck to lift a glass substrate without any sag. It applies special material that maintains its adhesion even if it is attached and detached to a substrate that can prevent a glass substrate from sagging to move glass substrates evenly without damaging them. It had put in significant amount of efforts to develop this sticky chuck. YAS applied its knowhow from Gen 8 deposition equipment to Gen 10.5 standard as well. “Gen 10.5 OLED deposition technology is already ready.” said Director Choi Myung-woon of YAS’ System Business Department. “It is not too different from current methods and it can steadily control Gen 10.5 glass substrates.” YAS is also planning to enter the market for Gen 6 deposition equipment and increase its market shares. It is mainly supplying sources that are keys to Gen 6 deposition equipment. These sources along with deposition equipment from other companies are applied to production lines of South Korean and foreign panel manufacturers. “Our goal is to steadily supply Gen 10.5 OLED deposition equipment and to supply Gen 6 OLED deposition equipment to domestic and foreign companies.” said Director Choi. “We are going to inform others about our technology within markets for large size and small size OLED panels.” Staff Reporter Bae, Okjin | withok@etnews.com
<Source: Etenws/전자신문>
|